If you are shopping for table legs, you will find that there are not many people making aluminum table legs. As such, a common question I get asked is "Why aluminum table legs?" Here I will provide information to help you understand why I use aluminum to handcraft my table legs, what the benefits are, and ultimately why you should consider them for your project.
Design
It is important to note that I am a designer, not a weld or fab shop. I have a MFA in design from the Sam Fox School of Visual Art and Design at Washington University in Saint Louis. This is important, because as a designer, I look at my product holistically, which means I am not simply creating a product that makes me money. I consider all aspects of the object that I am making, and foremost is the material! It is important to assess where the material came from, the unique qualities it possesses, and the environmental and social impacts it may havA question you may be asking, is "If aluminum table legs are so great, why doesn't everyone make them?" That's easy to answer! Aluminum is hard to work with, takes precision tooling, very accurate cutting and fabrication skills, and is expensive! In other words, the reason everyone makes legs out of steel, welds them up, and spray paints them, is because it's easy to do. It has become an industry standard, not because of the material, but because of the labor market. Working with steel is a very forgiving process, and it's easy to find workers that you can pay to do that job. Because you are welding the steel legs, the cuts can literally be inaccurate and have gaps, which the welds simply fill in.
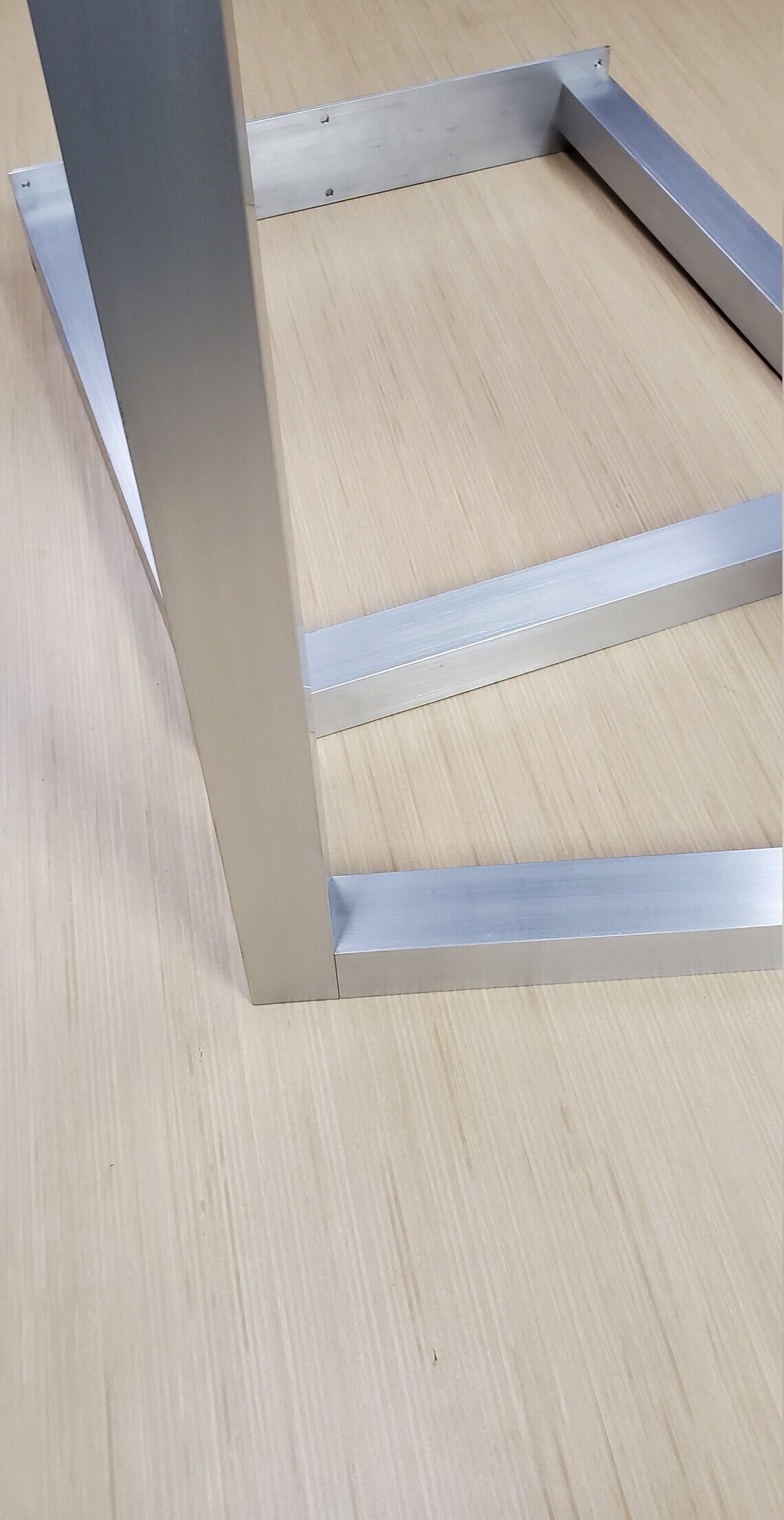
Strength Pound for pound, aluminum is stronger that steel. What this means is that if you build the same structure from steel and aluminum, which has the same strength, the aluminum structure will weigh 65% less than steel. In other words, the steel structure needs to be 65% heavier in order to be as strong as the aluminum. This means more steel material is need via material density, and shipping and handling costs are higher in terms of energy used to move the material around. Simply put, aluminum is stronger than steel. This is why I use architectural grade aluminum with a 1/8" thick wall.
Rust
Likely the biggest concern customers have with table legs is if the product will rust or not. This is especially true for outdoor tables. Aluminum does not rust. Steel does rust. It's a pretty simply comparison. However, many table makers spray paint their steel tables, or they market the rusty legs as something that is cool. Rusty metal can certainly be cool, until it leaves rust stains on your patio or carpet, so I reserve rusty metal for sculptures, not table legs.
Painting steel is problematic for a few reasons. First of all, the inside of the table leg is not painted, so you still have issues with the leg rusting over time, from the inside out. A simple change in temperature can result in the inside of the table leg being covered in condensation and we know that wet steel rusts fast. Another issue with painting steel is that if not properly prepped before painting, it is very likely that you will have rust under the paint. Since my first business was an industrial powder coating business (I powder coated mill-spec coatings for navy test apparatus brackets), I can tell you that most all weld shops do not know how to properly prep steel for painting because it requires a multi-step process of using etching acids and surface prep chemicals. Simply sanding the leg and spray-painting it does not fortify a long term, heirloom-quality finish. Though the steel leg may appear beautiful for a short amount of time, it will eventually explode with rust. I am sure you have seen this on older cars, lawnmowers, just name any object professionally made from steel that was painted and it will rust. A table leg welded up and quickly painted in the shop will certainly rust in this same way.
The benefit of aluminum is that it will not rust, even if you do not paint or finish it in any way. Most importantly, if you do purchase one of my powder coated aluminum table legs; you will never have to worry about it exploding with subsurface rust, ever. Powder coating aluminum is a very clean and environmentally friendly process. I never use spray paints because they contain volatile organic compounds (voc) that enter the atmosphere. I use voc-free powder coatings.
Style
If you look closely at various steel table legs and compare them to my aluminum table legs, there are a few important differences. The first is that steel square tube has rounded edges, while my aluminum has perfectly crisp edges. This gives my legs and much more "finished" and professional look. The second difference is that the steel legs have welds in the corners. Because of my unique building process, welding is not required and my legs look extremely clean, with perfectly fitting parts. I don't need welds to cover up any imperfections because they don't exist. The result is a perfect looking leg that visually compliments and supports your table, but is also beautiful as part of the whole that you are creating.
Environmental Impact
Both aluminum and steel can be recycled infinitely without degradation. However, keep in mind that a piece of 50 year old aluminum is going to be fully intact, 100% recyclable, while a 50 year old piece of steel is probably going to be rusted to the point that quite a bit of that steel is gone, eaten away by the chemical process of rusting, so it isn't necessarily 100% recyclable.
The production of steel is more energy intensive than the production of aluminum. The melting point of aluminum is 660 degrees. The melting point of steel is 1,540 degrees. The energy require to recycle, produce, melt steel and form it into the tubes used to make table legs is far greater for steel than it is aluminum. From a design perspective that puts my energy footprint as a top priority, this is one of the main reasons I choose to work with aluminum.
Once in the shop, both steel and aluminum are cut to size. Because steel is around 2.5 times denser than aluminum, steel is much, much harder to cut. Again, this requires more energy to cut, drill, and bend. It simply takes more energy to work with steel in the shop.
Steel table legs are welded. After welding, the welds are all ground off to make the finish smooth. Let's just think about this for a second. A steel table maker takes two pieces of steel, clamps them together, and welds the seams, filling in the joint with hot, liquid metal that builds up. That welding process takes a lot of energy. (When I rarely need to weld a tool or something that breaks on the homestead, my lights blink when the welder runs!) After welding, they grind off most of the metal they just melted into the seam, just to make it look pretty. If there are any small voids or holes that they missed, then they again fill that in with weld and regrind. This is an energy intensive process. I don't have exact data on this process, as far as the energy used, but it seems excessive to me.
In contrast, I cut my metal and that's the end of it. The aluminum is fairly easy to cut, it isn't extremely hard, and so my tools stay sharp for a very long time. Additionally, I don't have to use any nasty cutting liquids or grinders. I mean, where does all that metal go that the welders are grinding off? (I hope they wear respiratory protection!) And what sort of chemicals are in the cutting fluids?
Ok, so it sounds like I am pretty biased when it comes to aluminum table legs, but I just want to say this final thing. As a designer, I don't think aluminum is amazing because I work with it; I work with it because it is an amazing material. That's why you should buy aluminum table legs, not because I make them, but because they are a superior material for table legs. All table legs should be made from aluminum while steel should be reserved for things like bridges and buildings. You should buy aluminum table legs from me or from any other maker. Now, that doesn’t' mean the same table leg for a 20 pound side table should be used for a 500 pound dining table, there are different design considerations for that, which you can also read about on my blog.